Aluminum foil laminates are essential in various industries, particularly in packaging applications for food, pharmaceuticals, and medical devices. The proper testing of these materials is crucial to ensure they meet the required strength and durability standards for sealing. This article delves into the heat sealability of aluminum foil laminates, providing a comprehensive guide on how to test these materials following ASTM F2029, focusing on laboratory heat sealers and the testing process.
What Are Aluminum Foil Laminates?
Aluminum foil laminates are composite materials made by bonding aluminum foil with other substrates such as plastic films. These laminates are widely used due to their excellent barrier properties, providing protection against moisture, oxygen, and light. Understanding their heat sealability is crucial for manufacturers in determining their suitability for packaging purposes.
The Importance of Heat Sealability in Aluminum Foil Laminates
Heat sealing is a process where heat and pressure are applied to the materials to bond them together. For aluminum foil laminates, this is a critical step as the quality of the seal affects the overall performance of the packaging, such as its ability to maintain freshness and prevent contamination. ASTM F2029 outlines standard practices for determining the heat sealability of flexible barrier materials, including aluminum foil laminates, by measuring their seal strength.
Why ASTM F2029 is Important
ASTM F2029 provides guidelines for making laboratory heat seals and assessing the seal strength of flexible barrier materials. The standard emphasizes the importance of ensuring that the material’s construction and thickness are aligned with the required sealing properties. It also highlights the potential differences between laboratory-scale sealers and industrial-scale equipment, which may affect the seal’s integrity.
Understanding Laboratory Heat Sealers
What is a Laboratory Heat Sealer?
A laboratory heat sealer is an essential tool for testing the heat sealability of materials in a controlled, replicable environment. It allows manufacturers and researchers to simulate real-world sealing conditions and assess how well a material holds up under varying temperatures and pressures. By using a laboratory heat sealer, one can generate heat seal curves that help determine the optimal sealing parameters.
Selecting the Right Heat Sealer
When selecting a laboratory heat sealer, it’s important to ensure it meets the specific requirements for testing aluminum foil laminates. The Cell Instruments Heat Seal Tester Model HST-01 is an excellent choice for such tests, as it allows for precise control of temperature, pressure, and dwell time, ensuring accurate and repeatable results. The versatility of the HST-01 ensures that it can accommodate different sealing materials and conditions, making it ideal for a wide range of applications.
Conducting Heat Sealability Tests for Aluminum Foil Laminates
Step 1: Preparing the Samples
Before testing, it is essential to prepare the aluminum foil laminate specimens. The standard practice involves cutting the material into strips, typically 25 mm (1.00 in.) or 15 mm (0.59 in.), to be sealed. Proper sample orientation is crucial, as it can impact the sealing performance. Ensure that the sealing surfaces are aligned correctly.
Step 2: Setting the Heat Sealer
Using a laboratory heat sealer, set the temperature, pressure, and dwell time according to the requirements of ASTM F2029. Calibration and alignment of the sealer are necessary steps to ensure consistent and reliable results. Typically, both sealing jaws should be set to the same temperature to maintain uniformity across the specimen.
Step 3: Sealing the Samples
The heat sealer applies pressure and heat to bond the two layers of aluminum foil laminate. As per ASTM F2029, care must be taken to maintain the correct sealing conditions. The seals are then subjected to tests to measure their strength and integrity, such as the peel test using Test Method F88.
Step 4: Generating the Heat Seal Curve
A heat seal curve is generated by varying the sealing temperature and recording the seal strength at each temperature point. This helps determine the optimal temperature for the material’s heat sealability. The curve may also show how changes in temperature and pressure affect the seal’s strength, helping to refine the sealing process for mass production.
Key Considerations for Heat Sealing Aluminum Foil Laminates
Seal Strength and Testing
The key outcome of a heat seal test is the seal strength, which directly correlates with the material’s effectiveness in maintaining its integrity during storage and transport. By following ASTM F2029, you can establish a consistent method for measuring and improving the seal strength of aluminum foil laminates, ensuring they meet industry standards.
Calibration and Alignment
Ensure that the laboratory heat sealer is properly calibrated before conducting any tests. The alignment of the sealing jaws is crucial for producing accurate and reproducible results. Misalignment can result in inconsistent seals, undermining the reliability of the test.
Material Considerations
Different aluminum foil laminates have varying properties depending on their construction. For example, multilayer laminates with an aluminum foil layer require special attention to prevent issues such as sticking to the sealing jaws. Using appropriate jaw coatings, such as TFE-fluorocarbon/glass cloth, can help prevent this issue and maintain the quality of the test.
Conclusion
Testing the heat sealability of aluminum foil laminates is essential to ensure their performance in real-world applications. By following the guidelines set forth in ASTM F2029 and utilizing a high-quality laboratory heat sealer like the Cell Instruments Heat Seal Tester Model HST-01, manufacturers can ensure that their packaging materials meet the highest standards of quality and performance.
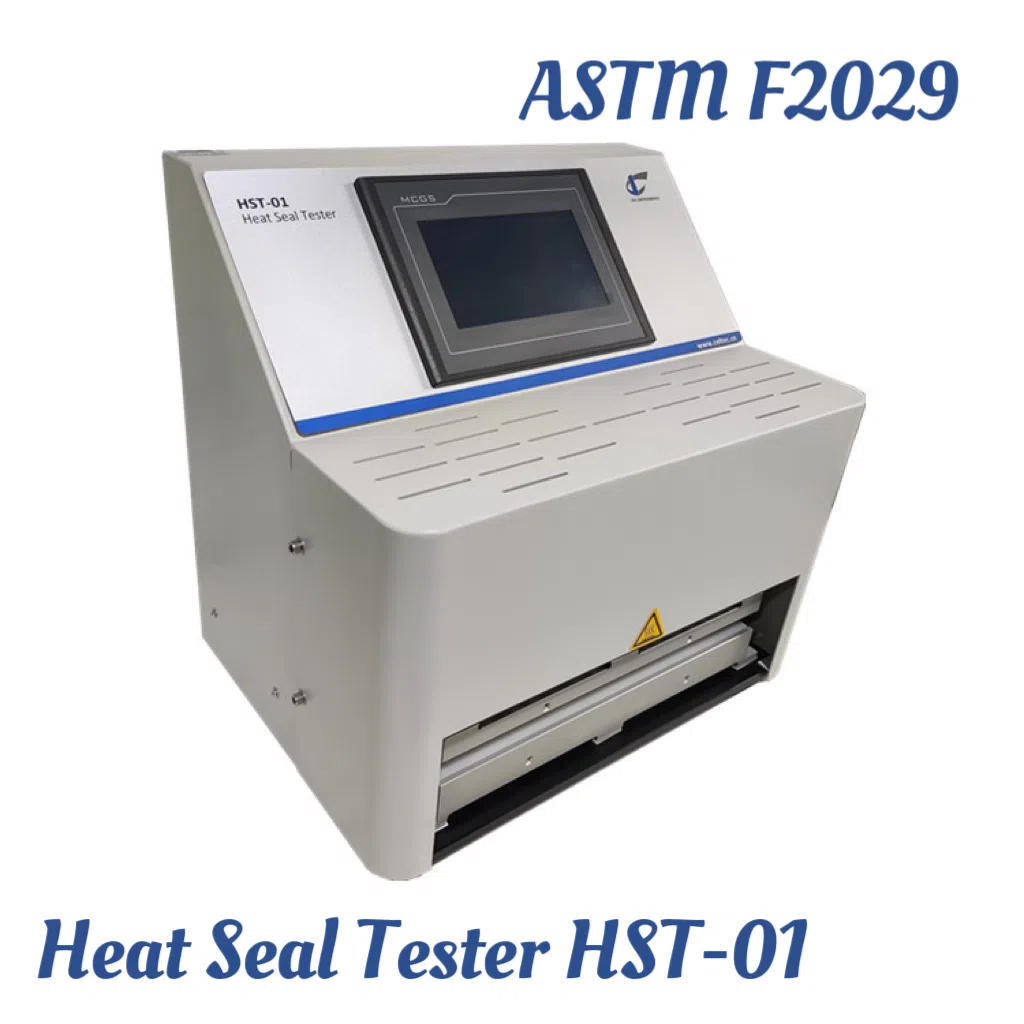